銀觸點(廣泛用于繼電器、接觸器等電氣元件)的焊接質(zhì)量直接影響導電性能與使用壽命,半自動化高頻焊接設備通過 “人工預裝 + 自動焊接” 的模式,在保證焊接精度的同時兼顧靈活性,尤其適配中小批量、多規(guī)格銀觸點的生產(chǎn)需求,以下是其工作流程與核心優(yōu)勢解析。
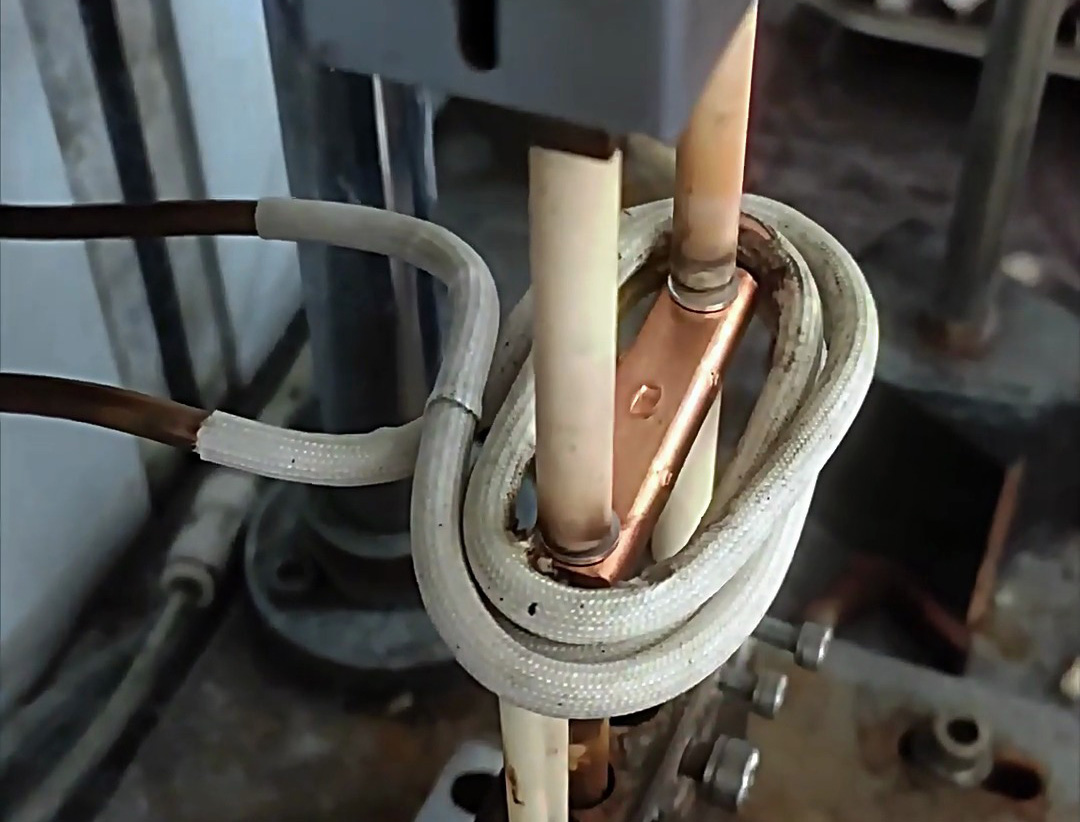
整套設備的操作環(huán)節(jié)清晰劃分 “人工輔助” 與 “自動核心”,實現(xiàn)效率與質(zhì)量的平衡:
人工前置操作(30-40 秒 / 件)
涂焊料:工人用專用工具在銀觸點或待焊基材(多為紫銅、黃銅)的接合面,均勻涂抹薄層焊料(常用銀銅焊料,熔點 650-700℃),確保焊料覆蓋整個接觸區(qū)域(厚度控制在 0.1-0.2mm,避免過多溢出);
觸點安裝:將銀觸點精準放置在基材預設位置(如銅片的觸點凹槽),用定位工裝臨時固定(防止焊接時移位);
裝夾模具:工人將預裝完成的工件放入高頻焊機的專用模具中,模具通過機械定位確保工件與感應線圈的相對位置固定(間隙 2-3mm,保證磁場集中)。
自動焊接環(huán)節(jié)(5-10 秒 / 件)
高頻加熱:啟動設備后,高頻焊機(頻率 30-60kHz)自動輸出預設功率(根據(jù)銀觸點尺寸調(diào)整,通常 5-15kW),感應線圈產(chǎn)生交變磁場,使銀觸點與基材接觸區(qū)域在 3-5 秒內(nèi)快速升溫至焊料熔點,焊料熔融并浸潤接合面;
保壓冷卻:加熱完成后,設備自動切換至保壓狀態(tài)(模具施加 5-10N 壓力,確保接合緊密),同時啟動風冷(或水冷),3-5 秒內(nèi)完成焊料凝固;
自動停機:焊接完成后設備發(fā)出提示音,模具自動松開。
人工收尾操作(10 秒 / 件)
工人取下工件,檢查焊口外觀(無氣泡、無虛焊),放入周轉(zhuǎn)箱,進入下一循環(huán)。
相較于全人工焊接(效率低、一致性差)和全自動化生產(chǎn)線(投入高、換型難),這套半自動化設備的適配性顯著:
質(zhì)量穩(wěn)定性:自動焊接階段的功率、時間、壓力參數(shù)完全固定,焊口強度波動≤5%(人工焊接可達 ±20%),銀觸點焊接后的導電電阻穩(wěn)定在 0.01Ω 以下(符合電氣元件標準);
柔性生產(chǎn):更換銀觸點規(guī)格(如直徑 3mm 換成 5mm)時,僅需更換模具與調(diào)整參數(shù)(10 分鐘內(nèi)完成),適合多品種、小批量訂單(全自動化線換型需 1-2 小時);
成本平衡:設備投入約為全自動化線的 1/3,且對工人技能要求低(培訓 1 天即可上崗),單班(8 小時)產(chǎn)能可達 800-1200 件,滿足中小廠家的生產(chǎn)需求。
某電器廠的應用數(shù)據(jù)顯示:采用該設備后,銀觸點焊接的合格率從人工焊接的 82% 提升至 98%,且因焊料用量精準(自動加熱減少浪費),材料成本降低 15%。
這套半自動化設備特別適合:
中小型繼電器、斷路器的銀觸點焊接(觸點直徑 1-10mm);
定制化電氣元件生產(chǎn)(規(guī)格多變,全自動化線不經(jīng)濟);
新產(chǎn)品試產(chǎn)階段(快速調(diào)整工藝參數(shù),驗證焊接效果)。
為保證焊接質(zhì)量,需注意:
模具精度:模具定位誤差需≤0.05mm,否則會導致焊口偏移;
參數(shù)校準:每批次生產(chǎn)前試焊 3-5 件,通過金相檢測確認焊層厚度(建議 0.05-0.1mm),再鎖定參數(shù);
線圈維護:每周清理感應線圈表面的氧化層(確保磁場強度穩(wěn)定),延長線圈使用壽命(可達 1 萬次以上)。
銀觸點半自動化高頻焊接設備的本質(zhì)是 “讓人工做擅長的柔性操作(預裝、取放),讓機器做精準的重復勞動(加熱、保壓)”,在保證焊接質(zhì)量的同時,兼顧了生產(chǎn)靈活性與成本控制,成為中小規(guī)模銀觸點焊接的 “性價比之選”。對于追求 “質(zhì)量達標 + 快速響應” 的廠家而言,這種 “半自動化” 恰恰是平衡效率與投入的最優(yōu)解。